How to Run an Electrical Safety Toolbox Talk
by Team Tradify, March 12, 2024
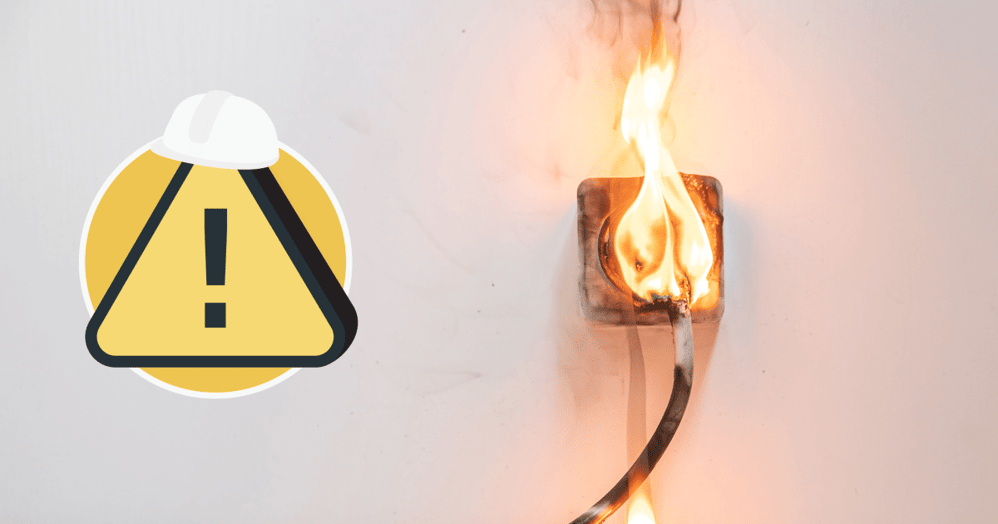
Table of Contents
Part of growing a successful electrical business is ensuring the safety of your entire team, including contractors, apprentices and employees. Providing your team with regular opportunities to engage in discussions about Health & Safety (H&S) helps to actively maintain a safe environment for everyone on site. One of the clearest ways to create this culture of safety is through regular electrical safety toolbox talks.
Run a smooth and productive toolbox talk with our free template!
Low on time? Skip ahead!:
1. What is a toolbox talk?
A toolbox talk is a focused conversation, typically held on-site, either daily or weekly, about the tasks ahead, plus any safety risks particular to the upcoming jobs. As electricians, you come into contact with specific dangers, which should be addressed before starting a new job. A toolbox talk is dedicated time for your team to express any concerns and discuss incidents that may have occurred since the previous session. It's also a chance to inform your staff of any policy or procedure changes. Regular toolbox talks also tick off a key part of your H&S compliance!
- 🇺🇸 Electrical Health & Safety Requirements for US Trade Businesses
- 🇬🇧 Electrical Health & Safety Requirements for UK Trade Businesses
- 🇦🇺 Electrical Health & Safety Requirements for Australian Trade Businesses
- 🇳🇿 Electrical Health & Safety Requirements for New Zealand Trade Businesses
Beyond legal obligations, fostering good communication and cooperation on-site is crucial for productivity and safety. Toolbox meetings are also a place where your team can have an informal chat about any concerns they have about upcoming projects and request additional support if needed.
Check the effectiveness of your current H&S processes and identify any gaps!
A toolbox meeting is more than a discussion about possible risks. It's an opportunity to cover a variety of H&S topics, including
- Discuss recent site review findings and required actions to manage uncontrolled risks.
- Talk about risks associated with upcoming tasks and the controls needed.
- Status of power supplies and connections.
- Review findings from recent events (injuries, illnesses, incidents, near misses) to prevent recurrence.
- Plan for emergencies.
- Cover worker and job induction procedures.
- Discuss training, competency, and supervision standards.
- Enforce specific site rules (e.g., no 3-step ladders, dry sweeping prohibitions).
- Outline the minimum required PPE and its usage.
- Manage hazardous substances.
- Ensure worksite facilities meet health and safety standards
2. How to run a toolbox talk
Ideally, toolbox talks will be run once a week. This allows for regular updates on work and risks, which will undoubtedly change throughout the project, or whenever a location changes. Monday mornings are recommended for these talks, as they set out the expectations for the week ahead. These meetings can be fairly informal, such as over a morning coffee, as long as everyone is present and engaged.
3. Advantages of toolbox talks
Toolbox meetings are a powerful leadership tool that enables worksite managers to showcase their commitment to safety, foster teamwork, and prioritise safety above all. These meetings are also vital spaces for encouraging workers to express their concerns or need for support.
To streamline your business and reduce admin, try Tradify. Sign up for a free 14-day trial or join one of our live weekly walkthroughs to see how we can optimise your business!
Related articles
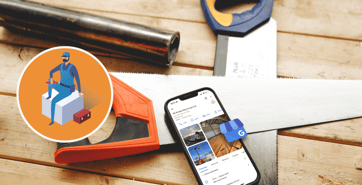
How To Set Up a Google Business Profile (for Trade Businesses)
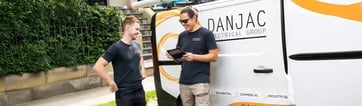
Aussie Electrician Reduces Admin Time by 95%
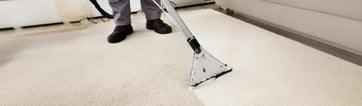
Squeaky Clean Scheduling for Pro Carpet Cleaning
Give Tradify a go for free!
Save 10+ hours/week on business admin with the highest-rated job management software for tradespeople.
With free one-on-one training and phone support, it's never been easier to get started.
