Who Can Test and Tag Electrical Equipment?
by Team Tradify, October 14, 2024
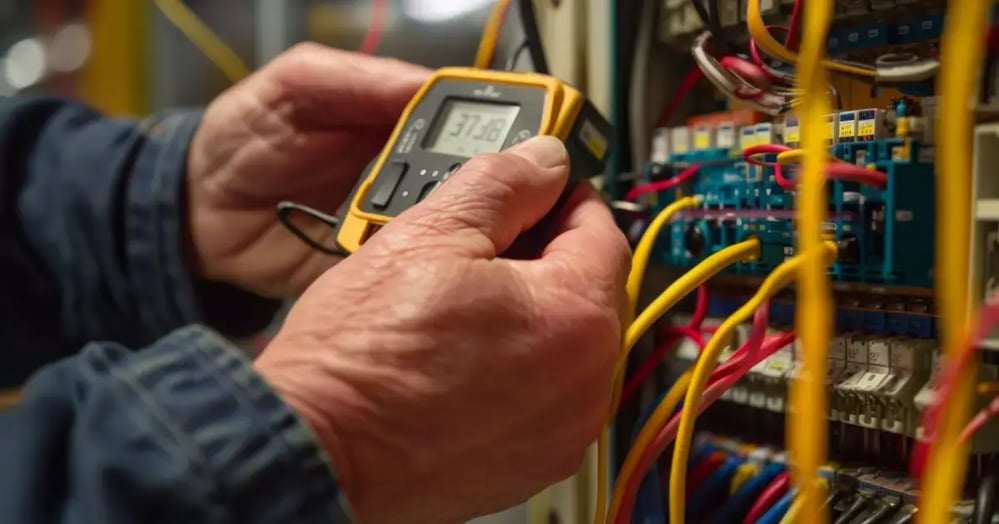
Table of Contents
Anyone who completes a short test and tag course can test and tag electrical equipment. Testing and tagging electrical equipment is required in Australia, New Zealand, and the UK to ensure the safety of workplace electrical appliances. In industries like construction, demolition, and mining, appliances must be tested every 3 months, while other workplaces may require testing every 1 to 5 years to meet their insurance requirements.
Want to give our job management software a test? Try Tradify free for 14 days!
Low on time? Skip ahead!
- What is a test and tag?
- Who can test and tag electrical equipment?
- What workplaces require test and tags?
- What type of equipment is tested and tagged?
- How often should I test and tag?
1. What is a test and tag?
Test and tag is a process in which a trained person visually inspects electrical appliances for any signs of damage, including issues with the flex, connections, guards, covers, and plug. After confirming the item is safe to test, they use a Portable Appliance Tester to check the appliance’s insulation, earthing, and polarity, and that it meets electrical safety standards. Once the testing is complete, the appliance is tagged with a label indicating it has been tested. The tag needs to include the technician's name, the test date, and the due date for the next inspection.
Technicians performing these tasks must be trained in using a Portable Appliance Tester and have specific knowledge of the risks associated with electricity and the types of appliances they may encounter. Although a formal certificate is (usually) not a legal requirement, it is highly recommended as it ensures that technicians understand the relevant regulations and can accurately assess the safety of electrical equipment in compliance with local legislative requirements.
United Kingdom: For the UK inspections must adhere to the BS 7671 IET Electrical Inspection Requirements.
Check out Tradify's digital Portable Appliance Testing (PAT) Report
Ireland: The regulations on Portable Appliance Testing in Ireland can be found in the Safety, Health and Welfare at Work (General Application) Regulations, SI 299, 2007.
/
ANZ: For Australia and New Zealand, the formal regulation code is AS/NZS 3760:2022.
2. Who can test and tag electrical equipment?
You don’t need to be an electrician or have an electrical background to test and tag electrical equipment (unless you're in Queensland, Australia, where a restricted electrical contractor’s license is required).
Anyone can perform electrical testing and tagging, though it is recommended to undergo training to learn regulatory requirements and how to properly use a PAT machine in order to be deemed a ‘competent person’. This can be achieved by completing a test and tag course, which usually takes 1 day and is offered by a registered training organisation.
A test and tag professional should have:
- Knowledge of visual inspection of portable electrical devices.
- The skill to differentiate between protectively earthed and double-insulated electrical equipment.
- Ability to conduct earthing continuity and insulation resistance tests on appliances according to standards.
- Ability to test safety switches or residual current devices (RCDs) per the regulations.
- Proficiency in using appropriate testing equipment and understanding test results.
- Knowledge of electrical safety legislation and regulations relevant to the testing location.
If a device is found to be faulty, it must be tagged to indicate electrical malfunction and taken out of action. Any electrical repairs should only be carried out by a registered electrical professional.
3. What workplaces require test and tags
In industries such as mining, demolition, and construction, businesses are mandated to test and tag their electrical equipment every three months due to the harsh conditions that can cause defects in appliances. Portable appliances, such as power tools and kettles, are frequently handled by workers and are more prone to damage due to harsh operating conditions. In most states and territories, regulations require appliances in hostile environments to be tested and tagged regularly (between 1 and 5 years) to prevent electrical hazards.
To meet their compliance and workplace safety obligations, businesses must:
- Conduct regular testing and tagging of electrical appliances and equipment to identify potential safety hazards.
- Use certified electricians or trained technicians who are proficient in using portable appliance testers and have undergone specific training in testing and tagging.
- Include visual inspections, functional tests, and the labelling and logging of all tested items as part of the testing and tagging process.
- Keep records of the testing activities, including the test date, technician name, equipment status, and next testing date.
- Once tested, a label indicating the tester's name, the test date, and the next scheduled testing date must be attached to the appliance.
It is recommended that most businesses demonstrate safe systems of work and maintain detailed records of all tests conducted by the technician.
4. What type of equipment is tested and tagged?
In short, any device that has a flexible cable, a removable plug and is not low voltage (not exceeding 50V) is tested and tagged. This includes extension leads, cord sets and portable RCD’s.
Generally, electrical appliances can be classed as either:
- Class I – this is an earthed appliance i.e. kettles, irons and toasters
- Class II – double insulated appliances, which are usually identified with a symbol (a square within a square) or with the words ‘Double Insulated’ i.e. most electric drills and hair dryers.
The formal pass/fail limits for electrical tests can vary depending on the category of equipment being tested. New equipment doesn't need to be tested - just visually inspected and tagged.
5. How often should I test and tag?
Testing and tagging should be done regularly, with a specific time frame depending on the environment in which the appliance is used. In high-risk industries like construction, demolition, and mining, testing is required every 3 months. The test tag colours change quarterly to help identify different testing periods throughout the year. In less extreme environments, testing may only be necessary every 5 years.
Ready to run a better business?
Tradify is used by thousands of tradespeople to build better lives and businesses. It gives you all the features needed to manage and grow a successful electrical business, including:
Sign up for a 14-day free trial. No credit card required. No commitment. Or pop over to one of our live demo webinars to see Tradify in action.
Related articles
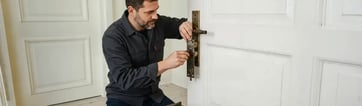
How to Start a Locksmith Business
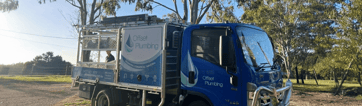
Offset Plumbing Backs Up Their Business
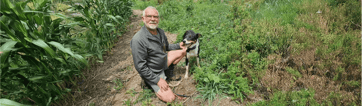
John Taylor Tracks Invasive Pests With His Dog, and His Jobs With Tradify
Give Tradify a go for free!
Save 10+ hours/week on business admin with the highest-rated job management software for tradespeople.
With free one-on-one training and phone support, it's never been easier to get started.
